Principle of Ultrasonic Cleaner
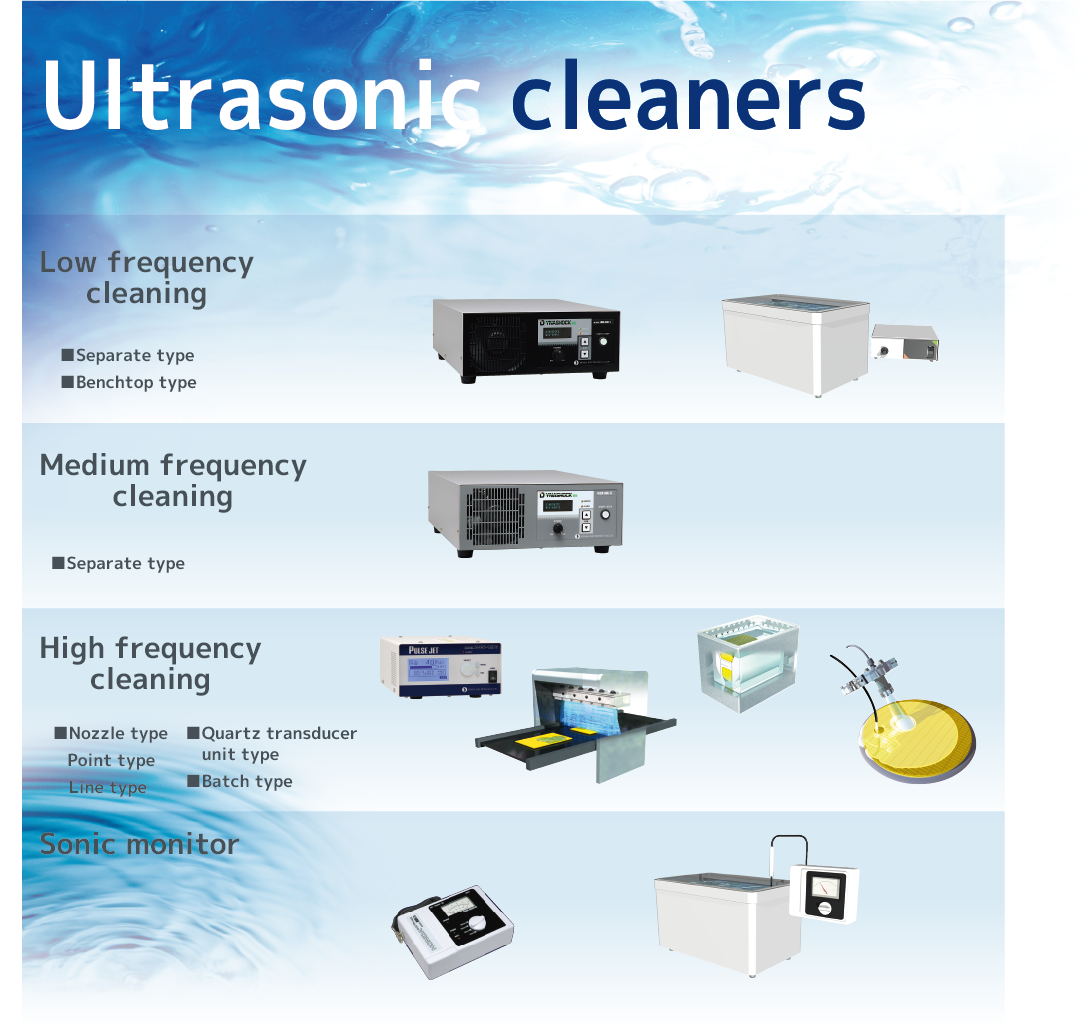
What is ultrasonic cleaning?
Ultrasonic cleaning to enhance the quality of industrial products
Ultrasonic cleaning is a technology that uses ultrasonic waves to vibrate water and solvents to clean oil, microscopic dust, dirt, and other contaminants that adhere to the workpiece to be cleaned. A familiar example is the ultrasonic cleaner used to wash eyeglasses at an eyeglass store. In industrial applications, ultrasonic cleaning technology is used in a wide range of applications, including removal of cutting oil, chips, buffing powder, and mold release agents from machine parts molds and tools, degreasing before plating, removal of flux from lead-free printed circuit boards, and cleaning of semiconductor parts, thereby contributing significantly to yield improvement and quality improvement of industrial products.
Ultrasonic cleaners are also used not only for "cleaning" but also for defoaming, degassing, dispersion, agitation, and crushing.
Principle of ultrasonic cleaning
Ultrasonic cleaning achieves its cleaning effect by combining the "physical effect" of ultrasonic waves with the "chemical effect" of the cleaning solution.
●Physical effect
Cavitation, vibration acceleration, and linear flow detach, disperse, and emulsify contaminants.
●Chemical effect
The chemical effect of the cleaning solution and the chemical reaction acceleration effect of ultrasonic waves dissolve and decompose contaminants.
How Ultrasonic Cleaning Works
Cavitation cleaning
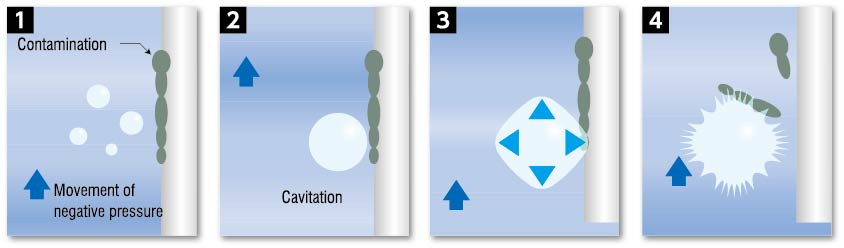
When powerful ultrasonic waves of 20 kHz to 100 kHz are emitted into a liquid, positive and negative pressures are alternately applied to the gas molecules. Gas molecules compressed by positive pressure expand violently the next instant due to negative pressure. This repetition causes the gas molecule to have a very high pressure at the time of compression, at the limit of which it bursts and disappears. The generation of this very high impact pressure is called the "cavitation phenomenon", and the effect of the shock wave when the bubbles burst acting on the workpiece to detach foreign matter is called the "cavitation effect".
This is mainly a cleaning action at low and medium frequencies.
In actual use of ultrasonic cleaners, the way in which cavitation occurs varies depending on the depth and type of liquid. Therefore, for good ultrasonic cleaning, it is essential to control these factors.
Cleaning by particle acceleration
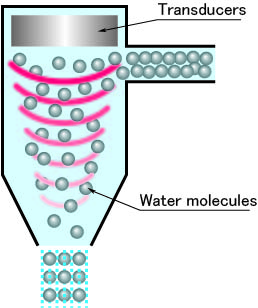
Ultrasonic cleaning by acceleration causes water molecules to be accelerated and strike the workpiece, and the impact causes particles to be stripped from the workpiece. The higher the frequency, the more effective the ultrasonic cleaning is, and it is effective in removing very fine particles with weak adhesion. The acceleration increases in proportion to the square of the multiple of the frequency, and the wavelength also decreases, making it effective against finer particles.
This is mainly a cleaning action at medium and high frequencies.
Cleaning by linear flow
When ultrasonic energy exceeds 0.5 W/cm2, a linear flow is generated away from the vibrating surface. This is thought to contribute to dust dispersion.
This is mainly a cleaning action at medium and high frequencies.
Cleaning action at low frequencies
■Batch-type cleaner
Degreasing and cleaning of metal and plastic parts, precision metal parts cleaning
Impact pressure from cavitation is effective in cleaning stubborn dirt. It is suitable for "general cleaning" such as removal of cutting oil, chips, buffing powder, and mold release agent from machine parts molds and tools, degreasing before plating, and removal of flux from lead-free printed circuit boards.
However, cavitation occurs in different ways depending on the depth and type of liquid, so it is essential to control these factors for good ultrasonic cleaning. Insufficient control can cause not only ineffective ultrasonic waves to be emitted into the liquid, but also damage to the vibrating surface (erosion), which can accelerate the deterioration of the vibration plate.
*Erosion: Erosion is a phenomenon in which the surface of soft materials such as aluminum is eroded by the physical force generated by the cavitation phenomenon of ultrasonic waves. The amount of erosion generated is proportional to the strength of the ultrasonic wave and inversely proportional to its frequency.
Standing waves (cleaning irregularities)
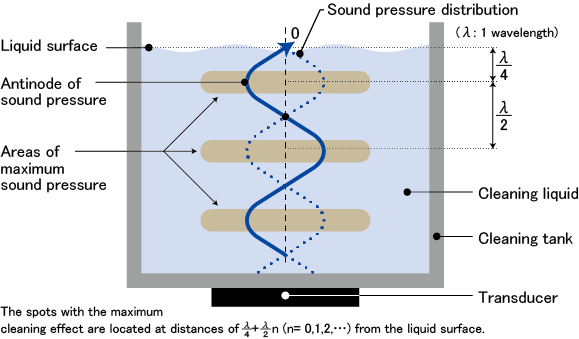
When ultrasonic waves are irradiated, standing waves are generated in the liquid in accordance with the frequency. (λ is one wavelength)
While dirt is removed, there is a possibility of damaging the workpiece. In order to reduce the influence of standing waves, oscillation of the workpiece and multi-frequency oscillation are also taken into consideration. It is necessary to determine the balance between the ease of stain removal and damage to the workpiece.
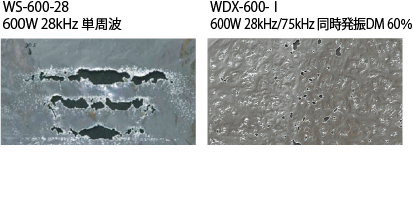
Product information on small ultrasonic cleaners by cavitation is available from Laboratory and General Cleaning.
Product information on large and separate ultrasonic cleaners can be found in the Industrial Use section.
Cleaning effect at medium and high frequencies
■Batch-type cleaner
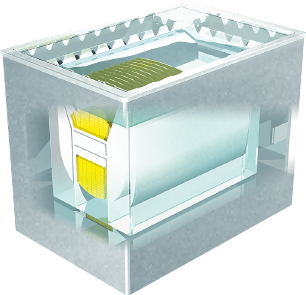
Batch cleaning of semiconductor wafers
This method cleans multiple numbers of semiconductor wafers at the same time by placing them in an ultrasonic cleaning tank in the MHz band.
(1) Many wafers can be cleaned at one time, which saves time.
(2) Relatively less cleaning liquid is required compared to the single-wafer method.
(3) Easier use of specific cleaning solution with double tanks.
When chemicals are used in a batch-type process, the dip-type cleaning method is often used, in which a double-layered structure of a cleaning tank and a quartz tank is used for indirect irradiation. The use of a quartz tank also avoids elution of metal ions and impurities and maintains cleanliness.
However, batch-type cleaning has been presented as a problem due to the increase in the size of equipment as substrates become larger and the re-adhesion of particles as substrate patterns become finer.
■Quartz Transducer Unit Type Cleaner
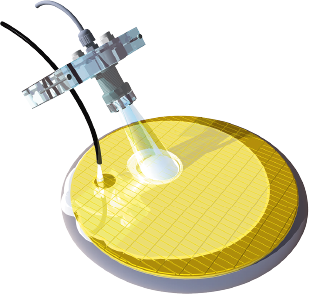
Next-generation cleaning for low damage and high cleanliness
In 2006, Honda Electronics developed the world's first quartz transducer unit type ultrasonic cleaner. In this system, semiconductor wafers are cleaned by superimposing ultrasonic waves on a quartz transducer unit. Compared to the batch type and nozzle type, the amount of chemicals used can be reduced, and the unit is clean because only quartz glass and chemical-resistant resin come in contact with the liquid while no rubber materials such as packing come in contact with the liquid. In addition, by changing the shape of the quartz transducer, it is possible to perform low-damage cleaning, large-area cleaning, and cleaning of hard-to-remove bevels (edge surfaces) and notches (notches on wafer edge surfaces), etc., to effectively clean wafers according to customer needs.
Product information on quartz transducer type cleaners is available from Semiconductor Industry.
■Nozzle type cleaner
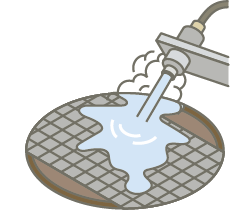
The world's first flowing water cleaning system developed
We were the first company in the world to develop this system in 1986. High-frequency ultrasonic waves in the MHz range are superimposed on the flowing water radiated from the tip of the nozzle to precisely clean the workpiece. The radiated water acts as a transport medium for the ultrasonic waves and at the same time, for the dirt that has been stripped off by the ultrasonic waves.
Product information on nozzle type cleaners can be found in Semiconductor Industry.
Products
We manufacture transducers from piezoelectric ceramic materials, a key technology in ultrasonic waves. We design and manufacture transducers with unique features that can only be achieved by in-house design, and incorporate them into our products with the highest performance in terms of delivery time, quality, and cost.
We offer a wide variety of ultrasonic cleaners to help our customers find the "perfect" machine for their needs.